Document Type
Article
Publication Date
2-2023
Department
Department of Mechanical Engineering-Engineering Mechanics
Abstract
As we enter the twenty-first century, the aviation sector is expected to thrive as flying becomes the primary mode of transportation between states or nations. With such a demand, there is a corresponding need to manufacture aircraft components. The study focused on recycling carbon fiber composites received from the STRATA company, which were cut-off/waste material generated during the manufacture of airplane components. The cut-offs were then reduced to powder form using a standard face milling machine in three sizes (90, 150, and 250 µm). After, the powder was utilized to fabricate vinyl ester composites with four weight percentages (10%, 20%, 30%, and 40%). The results demonstrate that the tensile strength of all composites had risen by 30.2%, 21.3%, and 17.6% for 90, 150, and 250 µm respective with the addition of 20 wt% of reinforcement. Furthermore, subsequently decreased with the additional reinforcement for all particle sizes. The compressive strength increased by 30% from 187.5 MPa to 244 MPa with 10 wt% of recycled carbon powder composite of 90μm particle size. However, samples prepared with 150 μm and 250 μm fiber size show approximately 17% and 1% increase in the compression strength with the addition of 10wt% of recycled carbon powder. A similar trend was observed for the flexural strength with an highest increase of 9% for 90 µm particle size with addition of 20 wt% reinforcement. Nonetheless, the SEM images revealed that the fiber–matrix bonding was weak, proved through the clean pullout fibers at the fracture surfaces.
Publication Title
Polymers
Recommended Citation
AlHarmoodi, K.,
Idrisi, A.,
Mourad, A.,
&
Abu-Jdayil, B.
(2023).
Utilization of Mechanically Recycled Carbon Fibers in Vinyl Ester Composites.
Polymers,
15(4).
http://doi.org/10.3390/polym15041016
Retrieved from: https://digitalcommons.mtu.edu/michigantech-p/17014
Creative Commons License
This work is licensed under a Creative Commons Attribution 4.0 International License.
Version
Publisher's PDF
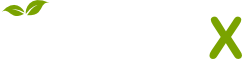
- Citations
- Citation Indexes: 2
- Usage
- Downloads: 52
- Abstract Views: 5
- Captures
- Readers: 8
- Mentions
- Blog Mentions: 1
Publisher's Statement
Copyright: © 2023 by the authors. Licensee MDPI, Basel, Switzerland. Publisher’s version of record: https://doi.org/10.3390/polym15041016