Experimental and Simulation Analysis of Temperature and Particulate Matter Distribution for a Catalyzed Diesel Particulate Filter
Document Type
Article
Publication Date
10-2015
Department
Department of Mechanical Engineering-Engineering Mechanics
Abstract
A multi-zone particulate filter (MPF) model from reference [1] was extended to analyze temperature and particulate matter (PM) distribution within each axial and radial zone of the filter substrate. A parametric study was used to determine the optimum required number of zones in the MPF model in the range of 5 × 5 to 20 × 20 zones for aftertreatment control applications. The MPF model with 10 × 10 zones was optimum and ran 12.2 times faster than real time. The 10 × 10 zone MPF model was calibrated using eighteen runs of data from a 2007 Cummins ISL engine that consisted of passive and active regeneration data sets for ultra-low-sulfur diesel (ULSD), diesel blend (ULSD) with 10 % biodiesel (B10), and diesel blend (ULSD) with 20 % biodiesel (B20) fuels. The MPF model was accurate, with maximum root mean square (RMS) error of 2.1 g for predicting PM loading and RMS error of within 10 °C for predicting temperature distribution within the filter. The PM distribution trends simulated by the MPF model were in good agreement with the experimental data measured using a terahertz wave scanner. The study of PM distribution during loading and at the end of PM oxidation (passive oxidation and active regeneration) showed that the PM oxidation by active regeneration leads to greater non-uniform PM loading of the filter compared to the passive oxidation as quantified using the uniformity index (UI) which was developed in the research to quantify the PM and temperature distribution.
Publication Title
Emission Control Science and Technology
Recommended Citation
Singalandapuram Mahadevan, B.,
Johnson, J.,
&
Shahbakhti, M.
(2015).
Experimental and Simulation Analysis of Temperature and Particulate Matter Distribution for a Catalyzed Diesel Particulate Filter.
Emission Control Science and Technology,
1(4), 255-283.
http://doi.org/10.1007/s40825-015-0022-y
Retrieved from: https://digitalcommons.mtu.edu/michigantech-p/5168
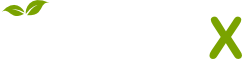
- Citations
- Citation Indexes: 9
- Patent Family Citations: 1
- Usage
- Abstract Views: 2
- Captures
- Readers: 6