Toward extreme high-temperature supercritical CO2 power cycles: Leakage characterization of ceramic 3D-printed heat exchangers
Document Type
Article
Publication Date
6-2022
Department
Department of Mechanical Engineering-Engineering Mechanics
Abstract
Future supercritical carbon dioxide (sCO2) Brayton power cycles demand high-performance gas-to-gas heat exchangers (HXs) operating under extreme temperature and pressure conditions at which most existing superalloy materials fail to function safely. Ceramic HXs are deemed excellent candidates for advanced sCO2 power plants as they can withstand high-temperature working environments. Particularly, ceramic 3D printing enables compact HX topologies employing complex and efficient heat transfer features. However, ceramic 3D-printed walls separating hot and cold flow streams are susceptible to a through-plane leakage inherent to a powder-based manufacturing process, including ceramic 3D printing. A potential leakage through ceramic separating walls poses a significant challenge in developing reliable ceramic 3D-printed HXs and could deteriorate thermal performance. In this study, various parameters, including feedstock slurry, 3D-printing direction, and post-processing conditions, are considered, for the first time, to characterize the argon gas leakage rate associated with alumina 3D-printed parts. Three 3D-printed ceramic structures of flat plates, curved tubes, and small-scale plate-and-frame HXs with various thicknesses are systematically studied to determine powder and ceramic 3D-printing conditions to eliminate the through-plane leakage. The results showed that an alumina 3D-printed plate with a thickness of 0.75 mm demonstrates a permeability of 6 × 10−4 milli-darcy. An alumina 3D-printed tube with a wall thickness of 0.9 mm revealed a permeability of 9.6 × 10−7 milli-darcy. Furthermore, leakage test results of functional 3D-printed modules showed a dependency on the 3D-printing direction. Particularly, alumina cell-scale HXs employing 1.5-mm-thick horizontal and vertical 3D-printed separating walls demonstrated impermeability and gas permeability of 7.2 × 10−5 millidarcy, respectively. Insights gained from the present study facilitate the development of complex ceramic 3D-printed HXs and other balance of plant components for next-generation high-temperature high-pressure sCO2 power cycles.
Publication Title
Additive Manufacturing
Recommended Citation
Bayaniahangar, R.,
Okoh, I.,
Nawaz, K.,
Cesarano, J.,
&
Bigham, S.
(2022).
Toward extreme high-temperature supercritical CO2 power cycles: Leakage characterization of ceramic 3D-printed heat exchangers.
Additive Manufacturing,
54.
http://doi.org/10.1016/j.addma.2022.102783
Retrieved from: https://digitalcommons.mtu.edu/michigantech-p/15879
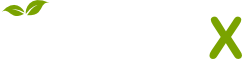
- Citations
- Citation Indexes: 7
- Usage
- Abstract Views: 27
- Captures
- Readers: 24
- Mentions
- News Mentions: 1