Mechanical properties of graphene nanoplatelet/epoxy composites
Document Type
Article
Publication Date
1-1-2015
Abstract
© The Author(s) 2014 Reprints and permissions: sagepub.co.uk/journalsPermissions.nav. Due to their high specific stiffness, carbon-filled epoxy composites can be used in structural components in aircraft. Graphene nanoplatelets are short stacks of individual layers of graphite that are a newly developed, lower cost material that often increases the composite tensile modulus. In this work, researchers fabricated neat aerospace epoxy (EPON 862 with Curing Agent W) and 1 to 6 wt% of two different types of graphene nanoplatelets (XG Sciences xGnP®-M-5 and xGnP®-C-300) in epoxy composites. These materials were tested for tensile properties using typical macroscopic measurements. In addition, nanoindentation was used to determine modulus and creep compliance. The macroscopic measurements showed that the tensile modulus increased from 2.72 GPa for the neat epoxy to 3.35 GPa for 6 wt% (3.7 vol%) xGnP®-M-5/epoxy composite and 3.10 GPa for 6 wt% (3.7 vol%) xGnP®-C-300/epoxy composite. The modulus results from nanoindentation followed this same trend. xGnP®-C-300/epoxy composites had higher tensile strength and ductility compared to similar loading levels of xGnP®-M-5/epoxy composites. The creep compliance for the neat epoxy, 1 to 6 wt% xGnP®-M-5/epoxy composites, and 1 to 6 wt% xGnP®-C-300/epoxy composites were similar. The two dimensional randomly oriented filler Halpin-Tsai model adjusted for platelet filler shape predicts the tensile modulus well for the xGnP®-M-5/epoxy composites and the three-dimensional randomly oriented filler Halpin-Tsai model works well for the xGnP®-C-300/epoxy composites. Per the authors' knowledge, mechanical properties and modeling for xGnP®-M-5 and xGnP®-C-300 in this epoxy system has never been reported in the open literature.
Publication Title
Journal of Composite Materials
Recommended Citation
King, J.,
Klimek, D.,
Miskioglu, I.,
&
Odegard, G.
(2015).
Mechanical properties of graphene nanoplatelet/epoxy composites.
Journal of Composite Materials,
49(6), 659-668.
http://doi.org/10.1177/0021998314522674
Retrieved from: https://digitalcommons.mtu.edu/michigantech-p/12812
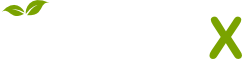
- Citations
- Citation Indexes: 104
- Policy Citations: 1
- Usage
- Abstract Views: 5
- Captures
- Readers: 164