Title
Fused particle fabrication 3-D printing: Recycled materials’ optimization and mechanical properties
Document Type
Article
Publication Date
8-1-2018
Abstract
Fused particle fabrication (FPF) (or fused granular fabrication (FGF)) has potential for increasing recycled polymers in 3-D printing. Here, the open source Gigabot X is used to develop a new method to optimize FPF/FGF for recycled materials. Virgin polylactic acid (PLA) pellets and prints were analyzed and were then compared to four recycled polymers including the two most popular printing materials (PLA and acrylonitrile butadiene styrene (ABS)) as well as the two most common waste plastics (polyethylene terephthalate (PET) and polypropylene (PP)). The size characteristics of the various materials were quantified using digital image processing. Then, power and nozzle velocity matrices were used to optimize the print speed, and a print test was used to maximize the output for a two-temperature stage extruder for a given polymer feedstock. ASTM type 4 tensile tests were used to determine the mechanical properties of each plastic when they were printed with a particle drive extruder system and were compared with filament printing. The results showed that the Gigabot X can print materials 6.5× to 13× faster than conventional printers depending on the material, with no significant reduction in the mechanical properties. It was concluded that the Gigabot X and similar FPF/FGF printers can utilize a wide range of recycled polymer materials with minimal post processing.
Publication Title
Materials
Recommended Citation
Woern, A.,
Byard, D.,
Oakley, R. B.,
Fiedler, M. J.,
Snabes, S.,
&
Pearce, J. M.
(2018).
Fused particle fabrication 3-D printing: Recycled materials’ optimization and mechanical properties.
Materials,
11(8).
http://doi.org/10.3390/ma11081413
Retrieved from: https://digitalcommons.mtu.edu/materials_fp/181
Creative Commons License
This work is licensed under a Creative Commons Attribution 4.0 International License.
Version
Publisher's PDF
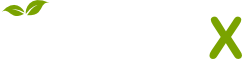
- Citations
- Citation Indexes: 179
- Policy Citations: 1
- Usage
- Downloads: 432
- Abstract Views: 105
- Captures
- Readers: 441
- Mentions
- News Mentions: 2
- References: 3
Publisher's Statement
© 2018 by the authors. Licensee MDPI, Basel, Switzerland. Article deposited here in compliance with publisher policy.